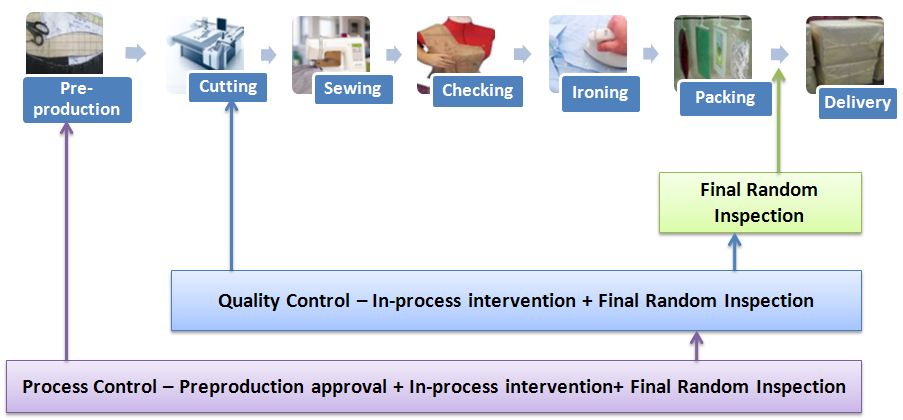
* Building Quality plans for styles based on customer's defined and expected requirements
* Garment quality testing
* Size set inspection and approvals
* Pilot / Preproduction inspection and approvals
* In-line Inspections and approvals
* Checker calibration
* Final random inspection - Sampling and Inspection by attributes as per
ANSI / ASQZ1.4 / ABC - STD 105 / DIN 40080 / BS6001 with AQLs as per customer requirement
Above mentioned are the different stage interventions provided for ensuring quality during garment production.This cycle of steps in the process of garment production ensures that
* The organisation is continously trained on understanding customer needs and the importance to focus on them.
* Subsequent stages in production are controlled and the garments that are produced will meet the stated and intended needs of the customer.
The manufacturer can rectify the defect and take preventive action to avoid recurrence.
The number of interventions depends on the order quantity and capacity of manufacturing facility. When the goods are ready for despatch, Final Random Inspection will be carried out to evaluate if the goods meet the defined requirements.
• It reduces the defects in the subsequent stages that it provides an opportunity to the manufacturer to initiate preventive action and improve productivity and Quality.
• The customer specifications / changes are rightly understood at the production floor
• The Quality parameters are in line with the specifications defined / established
• The goods manufactured and ready for despatch meet the Quality standards
• Pilot production approvals
• During Production – Quality Control
• After Packing – Final Random Inspection
Pre-production approvals are given on the samples produced in actual fabric, trims and in floor level production conditions. The product is evaluated against the approved sample / specifications given by the customer and reported to the customer where the deviation is observed to be critical.
When the goods are in production, Quality control procedure is followed with the number of interventions as agreed. When the goods are ready for despatch, Final random inspections are carried out to evaluate if the goods meet the defined requirements
• Subsequent stages in production are controlled and the garments that are produced will meet the stated and intended needs.